CCCB PRODUCTION DETAILS
The Company offers a complete range of Collector/Cathode Bar Machining Capabilities and Assembly, and will supply Ready to Install CCCBs.
The Steel Bars are Manufactured from imported Hot Rolled Steel, or from Australian Made Hot Rolled Steel Slabs, Flame Cut into specified Cathode Bar Sections.
The Rolling Processes for BOTH imported and locally sourced bars, produces Cathode Bars which are Rolled in the same Direction as the Electrical Current will flow in the Operating Pot. That is, the favourable Grain Orientation is Independent of the Steel Production Process.
The Steel Grade utilised is the Steel Grade 1006, (0.08% C Max). Typical Carbon contents as shipped, range from 0.04% to 0.06%. Grade 1006 is the Steel Grade Specified by all the Smelter Groups and Companies Worldwide for the Cathode Bar applications.
However, the Flame Cut Steel as it shipped from the Steel Works is considered by some smelters as not suitable for the Cathode Bar Application without further processing – as the result of the Flame Cutting Process. Thus, the Flame Cut Bars must be Treated at ASSS – to “convert” the Flame Cut Bars into Steel Cathode Bars which meet All Specifications as set down by the Smelters for Edges/Corners, Surface Finish, and Twist – for both Steel and CCCB Cathode Bars.
The Australian Steel, as received by ASSS, is converted by what is Termed the “ASSS Conversion Process” (ASSSCP), which process will produce bars which will conform to the existing Dimensional Specifications set down by the various Smelter Companies.
The ASSSCP was Jointly Developed by DHDS Company and Warren Mockler.
The ASSSCP provides Flexibility to our Smelter Clients. For example, with the recent advent of Copper Plated Cathode Bars (CPCBs) it is preferred that the Steel Face under the Copper Plate not be Cornered so that a Maximum Interface Area is created between Steel and Copper. That is, the Corner R is approximately 0 – but the “Bottom” Steel Radii is the Standard either R10 or R15.
Another example - if Sealing Conditions demand an improved flow of Molten Cast Iron into the Cathode Block Slot. The ASSSCP will produce Chamfered Top Corners into the Cathode Bar while maintaining the R10 - R15 Corners at the Bottom (of the Cathode Block Slot).
The DHDS (Deep Hole Drilling Specalists) facility includes CNC and Conventional Machines, with a Capacity to Drill Hole Diameters from 2 to 152mm. It is possible to Machine On and Off Centre Drilling with Work Pieces of up to 16 tonnes.
With CCCB production, the Company targets a clearance fit between copper insert and hole diameter of between 0.10 and 0.20mm. Tolerances are dictated by the copper insert diameter and the quality supplied. 100% of CCCBs produced are checked and measured to ensure Customer Tolerances are met. Copper inserts are measured and the holes are then drilled to match the insert diameter to provide the tightest possible clearance between the insert and the hole.
As Shipped / Delivered Steel Cathode
Deep Hole Drilling of the Steel Bars for Insertion of Copper Bars.
Finished Copper Cored Cathode Bars (CCCB
Our delivered and installed CCCBs have performed extremely well under normal Pot Room Operating conditions. One of our customers has seen a 130mV CVD gain (as compared to the previously used Steel Cathode Bar) – with an accompanying Pot Life improvement from 2100/2500 days to 3000/3500 days.
NOTE: The Steel was Australian made 1006 Grade, Flame Cut Steel Processed at ASSS.
The Company has been producing CCCBs since 2003, and has produced in excess of 50,000 Finished Assembled CCCBs.
Our Client List includes ALL the Australian – N.Z. Operating Smelters viz::
- Alcoa Portland Aluminium
- Tomago Aluminium Company
- Boyne Smelters Ltd
- New Zealand Aluminium Smelter Ltd
- RTA Bell Bay
ROBOTIC MANAGEMENT OF CCCB DRILLING, MACHINING AND CLEANING.
The introduction of robots into our operations has increase both the Productivity and Safety of the ASSS Processes. The Robots ensure that all the Individual Production Processes within the Production Cell are working Simultaneously, such that the Robots feed Bars to the Individual Production Units, and Manage the Drilling, Machining, Cleaning and Assembly, and Finally Stack the Completed Bars, prior the Bars moving to ether the Cathode Sealing Operations Area, or to the Despatch Area in preparation for Shipment to the Smelter Customer.
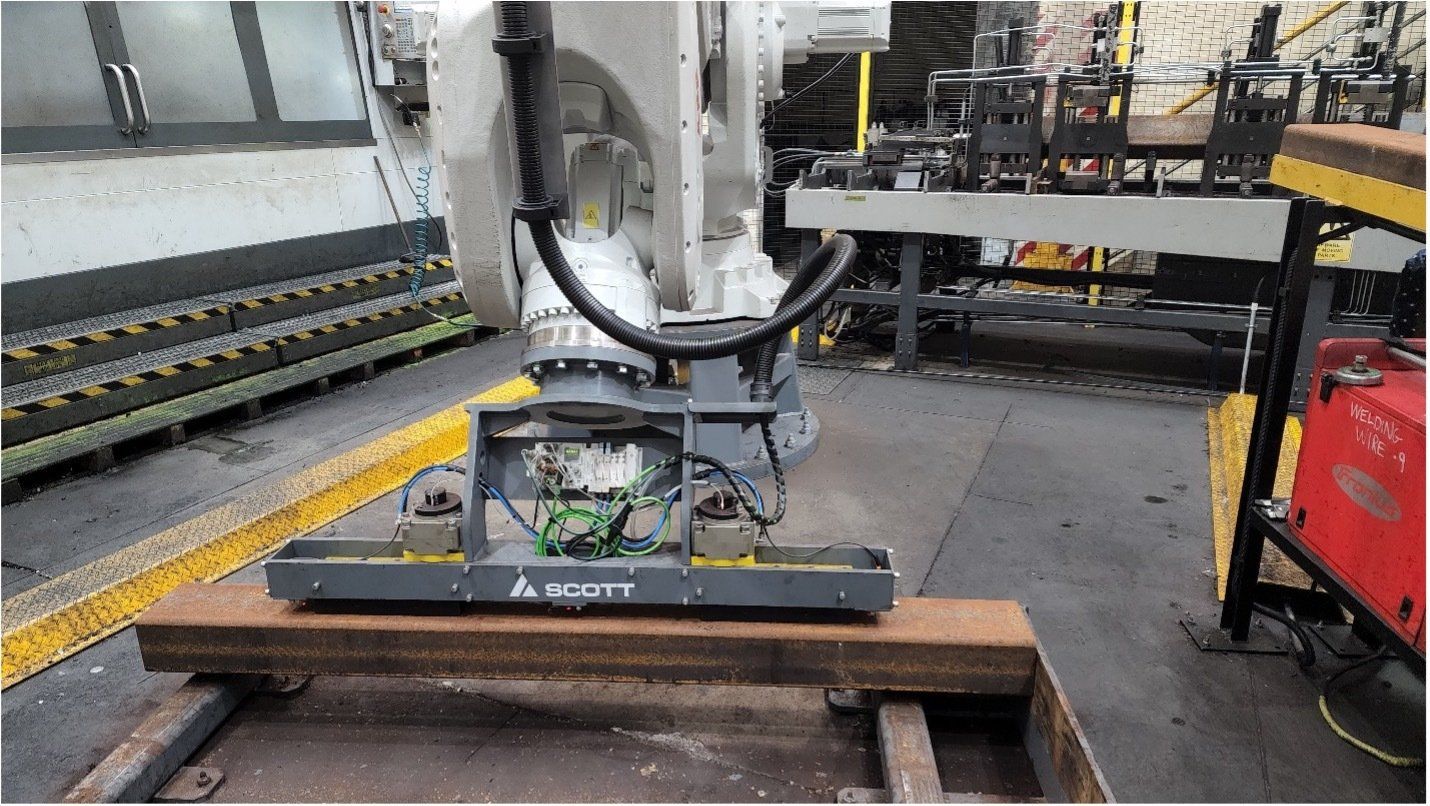
Cathode Bars are placed in the Infeed/Outfeed Station via forklift. The first Operation for the Robot is to pick a bar and place it at the Drilling Station which has Dual Drilling Spindles, nominated as Side A and Side B.
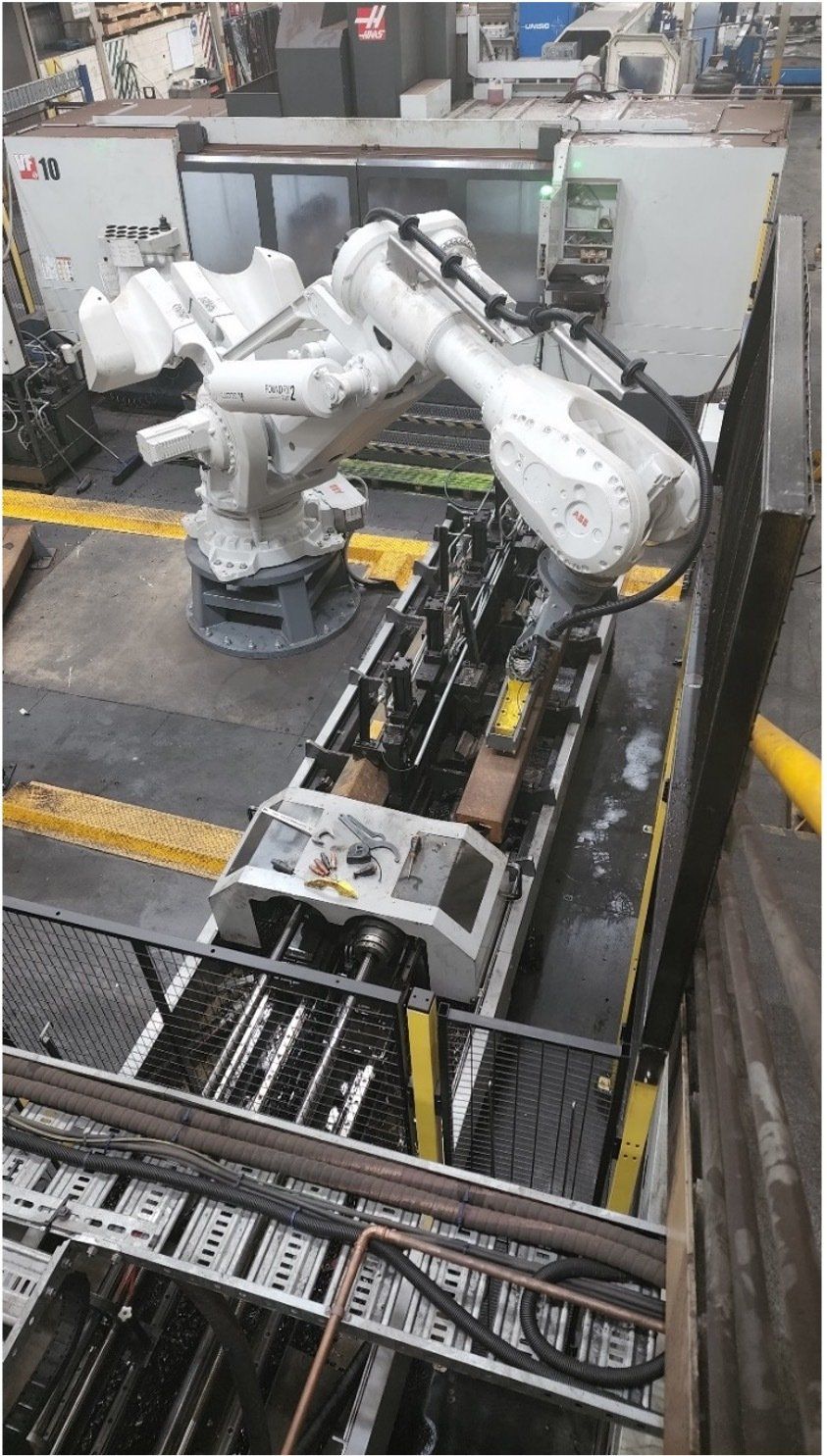
This Image displays the Robot Unloading a Cathode Bar from the TSDHDM (Twin Spindle Deep Hole Drilling Machine) to be placed into the Adjacent Cleaning Station.
This machine a Cathode Bar in the Twin Spindle Deep Hole Drilling Machine specifically designed to drill collector bars.
Having a Twin Spindle Drilling Machine allows for a continuous drilling operation, that is, while one side is drilling the other is being unloading and reloading by the Robot.
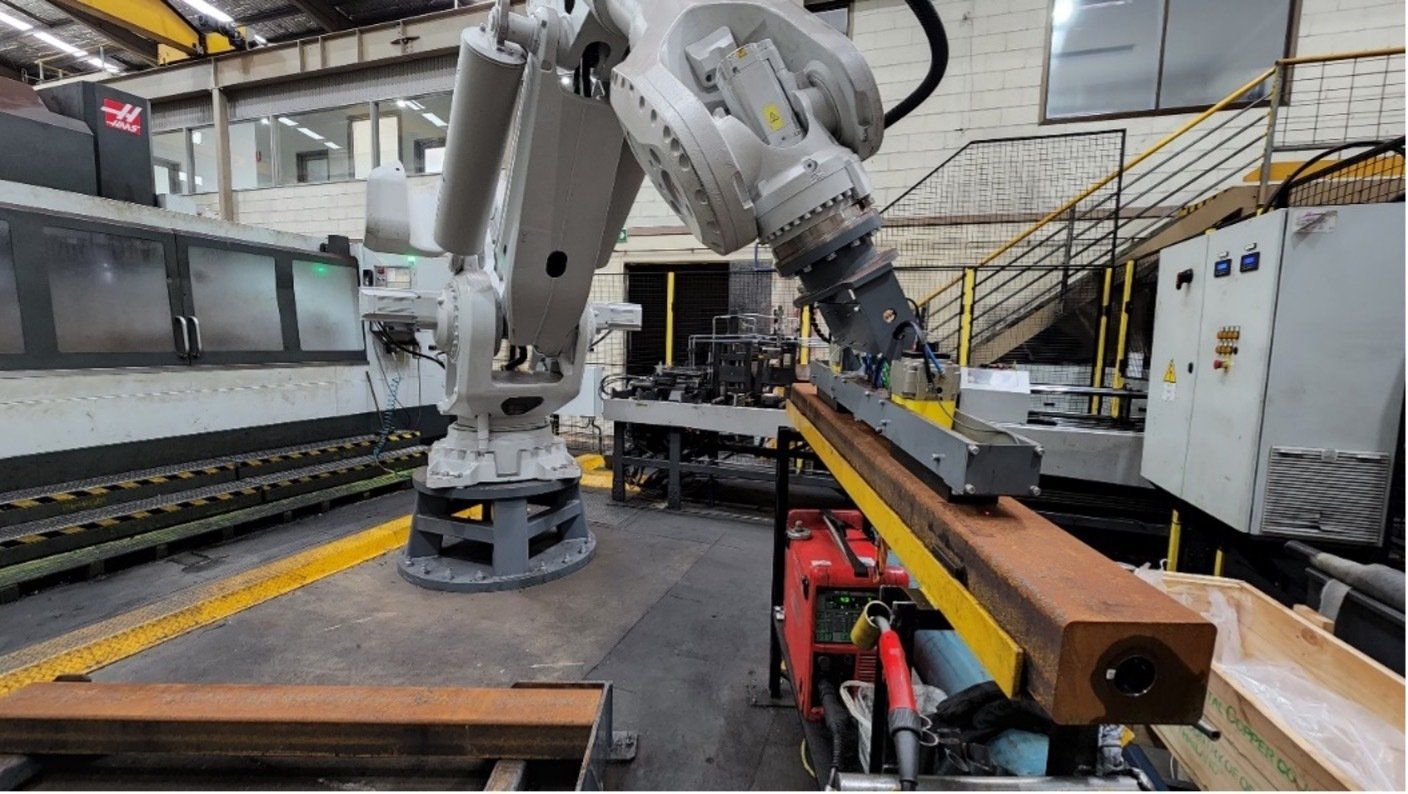
Once the Cathode Bar is Drilled/ Cored, the Robot places it into the Cleaning Station, where all Oil Residues are removed. This is followed by a Drying Operation - this is to ensure that there is No Contamination in the Core Holes which would interfere with the Electrical Connection between the Copper Core and the Steel Cathode Bar.
At this point in the Process, the Copper Core and Core Hole Diameters are measured and recorded. The Copper Core is then Inserted under Pressure, and often Welded into position - to whatever the Customers Specification requires.
The Next step in the Process is the External Machining of the Bars (Machined Ends and Bolt Holes) _
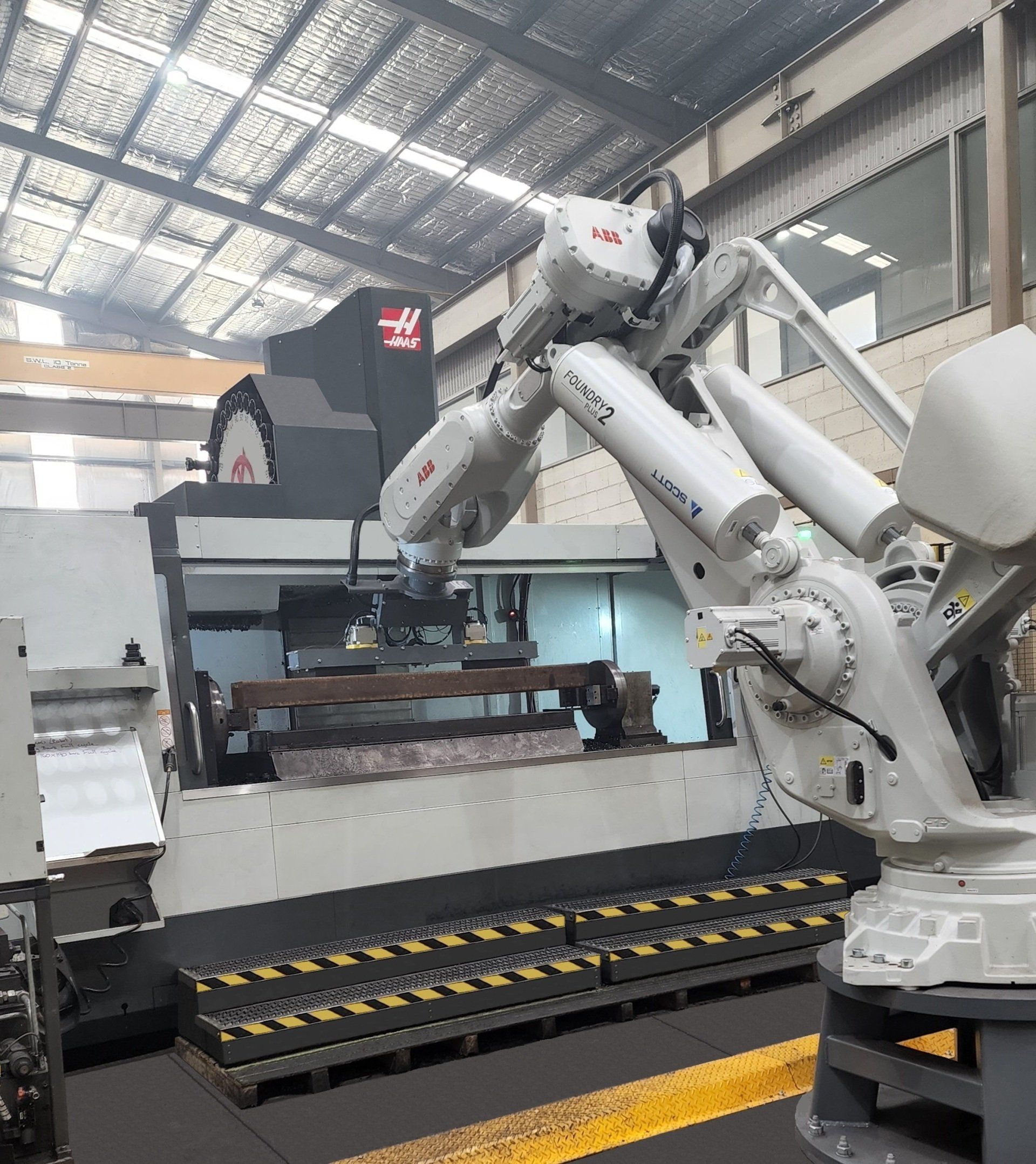
This Image displays the Robot placing a Cathode Bar into the Vertical Machining Machine wherein all the External Machining of the Bars for Electrical Contacts (Flats) and Bolt Holes takes place.
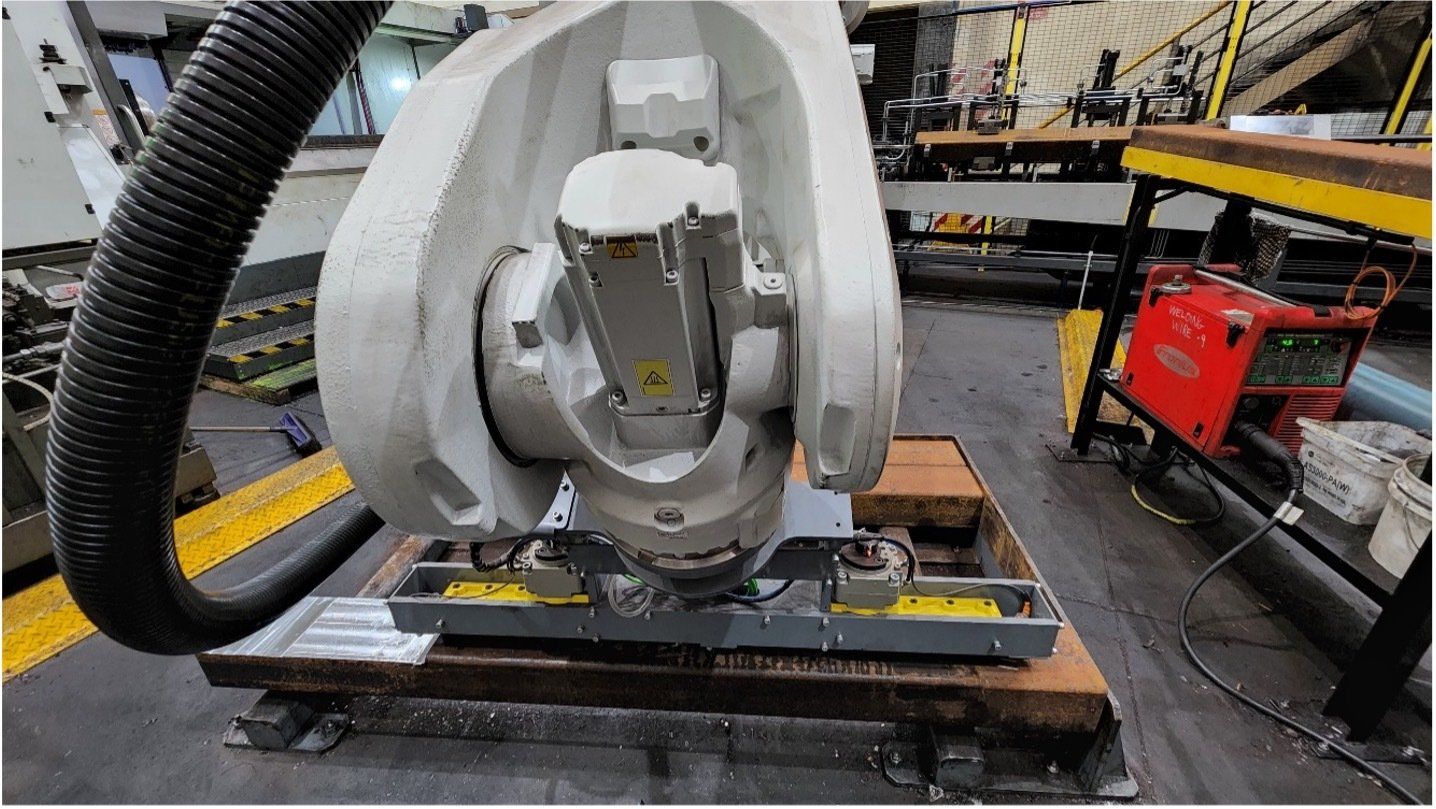
From the Vertical Machining Centre the Completed/ Finished Copper Cored Cathode Bar the Robot moves the Bars back to the In Feed / Out Feed Station. From here the Stacked Pallets move either to the Cathode Sealing Area or the Despatch Area in preparation for Shipment to the Smelter Customer.
As indicated in the above Pictures, the whole Drilling, Machining and Cleaning Operation is carried out Automatically without Human involvement.
The Operation needs only to stop for the Replacement of Worn Tooling and other consumables used. in the Process.
CATHODE BLOCK PROCESSES AND SEALING OPERATION
The Company commenced Cast Iron Rodding/Cathode Block Sealing in early 2013. At that time, the principal customers were the two Alcoa Smelters – Portland and Point Henry.
Currently, Rodding Services are provided to 3 of the RTA Smelters in addition to Portland:
- Boyne Smelters
- NZAS
- Bell Bay Aluminium
CATHODE SEALING OPERATIONS ROOM
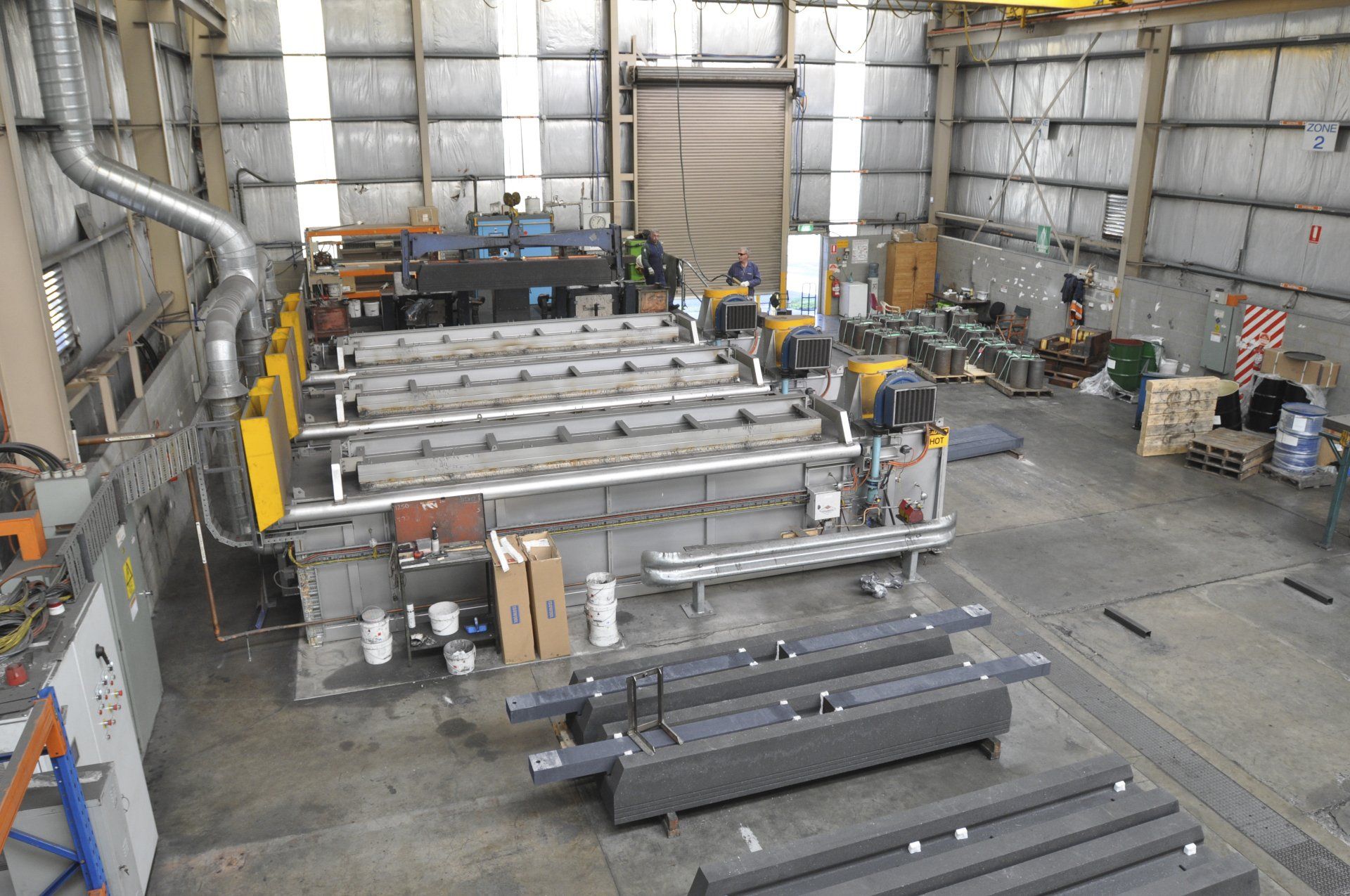
The Process commences with the Shot Blasting of each CCCB to remove all traces of Rust and Scale, to ensure a Low Resistivity Interface will exist between the 1006 steel and the Cast Iron Rodding Material.
The Shot Blasted Bars are then Positioned into the Cathode Block Slots.
The "Assemblies" are then Preheated to a Temperature of 450oC - to ensure the Fluidity of the Molten Cast Iron is sufficient to penetrate the narrow gap between Bar and Block at the bottom of the Slot.
Good Sealing is achieved without the addition of Ferro Phosphorus to the Cast Iron Melt.
The 3 Pre-Heating Furnaces have a Combined Capacity of up to 2 Assemblies per Hour, depending on the Size of the Cathode Assemblies.
SEALING OF CATHODEBAR INTO CATHODE BLOCK WITH CAST IRON
FINISHED CATHODE “ASSEMBLY”
CRATED CATHODE ASSEMBLIES READY FOR SHIPMENT
ASSEMBLIES STACKED INTO A CONTAINER